By applying the principles of lean continuous improvement, a team of students is improving the campus community while building skills essential to professional life.
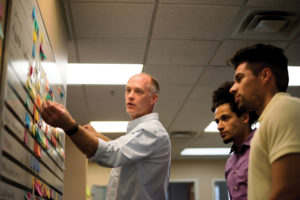
While “continuous improvement” is a concept more often associated with business or manufacturing practices than with higher education, the concept has found a natural home at Berea College. Perhaps this is a result of our history of “plain living,” the ongoing need to harness our financial resources to support our no tuition promise, or our commitment to lifelong learning. Whatever the reason, continuous improvement at Berea makes sense while saving dollars.
Derrick Singleton, vice president for operations and sustainability, and Richard Smith, the College’s previous continuous improvement (CI) manager, introduced the concept about four years ago. Simply put, continuous improvement seeks to eliminate waste in everyday processes and improve the overall quality of life for students, staff, and faculty.
“There are several facets of the continuous improvement program,” said Aaron Beale, continuous improvement manager at Berea College since October 2016. “However, our primary goal is to help faculty, staff, and students serve our mission by helping individuals achieve what motivates them to be a part of Berea College.”
Beale works with a team of students to enhance Berea College by pursuing three goals: driving the mission of the college, supporting the College’s financial sustainability, and demonstrating respect for people by increasing the well-being of faculty, staff, and student workers. All three are achieved by the application of continuous improvement. “Continuous improvement aids the students, staff, and faculty by removing the waste from our processes,” according to Logan Gardner ’18, a member of Beale’s continuous improvement team.
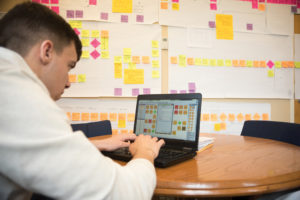
Beale utilizes lean-management tools as the basis for the continuous improvement program. While lean management first came into wide use in the United States in the 1980s in manufacturing, Beale stated that, “today, it can be and is used in various areas ranging from healthcare, legal practices, higher education, and government. Anywhere there is a process, lean can be applied.” Still, he acknowledges that using lean in a college setting puts quite a twist on its factory origins. “We look at efficiency,” said Beale, “but more importantly, we focus on increasing the time available for students, staff, or faculty to do their best work.”
When evaluating a project, Beale and his team of students start by asking the client what is not working within their current process. What aspect of their work causes them “pain?” Pain points, in the language of continuous improvement, are often surrounded by “non-value added steps.” At this point, the CI team uses value stream maps to identify all the steps in a process, and determine which steps to retain because they add value and how to eliminate the non-value added steps.
Qamar Shaker ’17 said, “Continuous improvement helps elevate the way individuals think. It teaches them to stop saying ‘I’m here and I have to do this.’ Instead, the person starts to ask, ‘Why am I working in this way?’ which opens up the various ways they can alleviate the difficulty within the tasks they perform.”
Since the program began, Berea College has realized a combined hard and soft savings of over $1.4 million by applying lean techniques. However, in many cases the less quantifiable rewards outweigh the financial benefits. One instance in which CI saved the College money and helped support its mission was by changing how work orders for residence hall rooms are completed over the summer and when students arrive in the fall. Historically, an influx of work orders would be submitted to the Facilities Management (FM) office for maintenance in the residence halls. FM technicians would inspect the rooms, acquire parts, and would occasionally have to bring in external contractors to finish the repairs. The CI team helped FM eliminate the waste in that process by being proactive. “We shifted that model around, and had our technicians go in as soon as school got out, and used the data we collected over the years to create a checklist of likely repairs,” said Beale. “Now, FM pre-orders needed supplies and moves through proactively to make repairs before the students arrive.” This led to savings through reduced gas and labor costs by decreasing the number of trips needed to complete repairs. It also reduced the need to hire contractors and cut the wait time for procuring materials. But, the biggest gain was in customer satisfaction as students came back to fully functional rooms, which eliminated an unnecessary source of stress from their lives. And, if there is one thing college students need less of, it is stress.
Getting Results
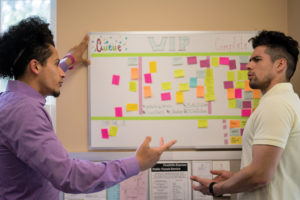
In response to student requests, Dining Services extended its operating hours. That meant students with labor positions in Dining Services worked well into the night, sometimes returning to their residence halls past midnight. By removing unnecessary steps and creating a system of standard work, students saw their work day shorten by more than an hour—a quality of life improvement that gave them more time to sleep or prepare for class the next day. “The main mission of that project wasn’t cost savings, but to get students home at a more reasonable time,” said Beale.
An ongoing project that Beale and his team continue to work on is finding ways to increase recycling on campus. The first phase began with Sustainability Coordinator Joan Pauly looking for ways to improve recycling in the dorms. At that time, the focus was on making it easy for students to put waste materials into the proper recycling container. That involved creating consistent signage and finding recycling bins that would work well in the dorms.
Pauly said the success of this part of the program has been easily quantifiable. “From July 2015 to March 2016, total recycling in the residence halls amounted to 164,861 pounds,” she said. “In the same period the following year, with the new bins and signage, the total amount recycled increased by 24,767 pounds to 189,628.” This success, however, put additional strain on the recycling team—led by Recycling Coordinator Kevin Long. His team is responsible for transferring the material collected at the residence halls to the company that handles removing recycled material from campus.
As a result, a second phase of the project began in the fall of 2016, when Beale and CI team member Emmanuel Lomeli-Garcia ’18 began working with Long and his team of students at FM to apply lean management tools to both recycling collection and its processing. “This involved physical adjustments to the workflow,” said Beale, “and the application of 5S (a key lean tool, 5S stands for Sort, Set in Order, Shine, Standardize, and Sustain), visual management, and the creation of standard work.” Because of these efforts, Long’s team at recycling was able to process 3,825 pounds of mixed recycling in December 2016, up from 2,442 pounds in December 2015. In the four months prior to the launch of the lean process, the monthly collection average in the residence halls was 2,243 pounds. March 2017 saw total recycling collected weighing in at 40,638 pounds, the highest monthly total this fiscal year. Not only are the numbers up, but Long’s recycling students now have time available for more “value-added” outreach tasks that support the College’s commitment to sustainability.
Getting the Best to Campus
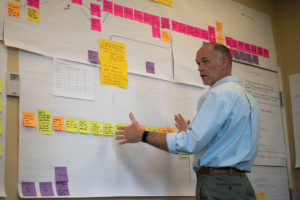
The impact of continuous improvement is felt even in areas that do not directly involve students. Beale and his team are also helping refine the hiring process within the Human Resources office by working with Director Steve Lawson and Sheri Gordon, human resources business partner. Because of the College’s historic commitment to diversity, having a diverse pool of job applicants is especially important. Gordon said, “The faculty and staff of Berea College should mirror the diversity of the student population. Staff and faculty who come from various backgrounds and experiences can bring a multitude of skills and perspectives to our community. Integrating these elements enhances the learning process for all involved.”
According to Lawson, working with the continuous improvement team was itself a rewarding experience. “[The process] allows you to step back from the challenges of getting the work done and look at the work objectively,” said Lawson. “Sometimes learning can be finding and admitting to the waste in the process.” For his team, Lawson said one of the biggest eye-openers was calculating how much time it takes to physically execute a task, ‘touch time,’ versus how much time may pass before all the steps are completed for that task, ‘cycle time.’ Seeing the difference between touch time and cycle time allowed the staff members to identify constraints and eliminate wasted efforts.